Custom Metal Forging
When you need a custom metal part, you need a part that's strong, leak-resistant, low-cost, a superior surface condition, a precise replica of your design and can be produced repetitively and have close tolerances, close die forgings are what you want.
Close Die Forging is an inexpensive and efficient way to manufacture metal parts and it can also be made in many different metals, it depends on the application. At Queenta, we can take any design and metal and turn it into a metal component. These are from aerospace metal part to a metal part used in oil drilling equipment, military to marine part and even by not all, water or gas valve parts.
Some examples of forged parts we can manufacture include:
Door and window hardware parts as well as all types of Lock parts
Pump and Valve bodies and parts and even valve handles
Archery bow clamps, risers, and various other parts
Many different electrical parts, electrical contacts and even Pole Line Hardware
Nuts of all shapes and sizes
Commercial weighing equipment and parts
Various parts for the Oil and gas industry
Gears and pulleys
Water meter parts
Hydraulic cylinder parts
Synchromesh parts - gear boxes
Fire sprinkler parts and fittings
Faucet and shower parts
Impellers and propellers
Various fan blades
Cable Fitting parts
Hydraulic fitting parts
Pipe and tube fittings
Gas fittings
Gas valve parts
Sports and recreational equipment parts such as Golf putter heads, etc.
There are many more parts from various industries that we supply but they are too numerous to mention.
Queenta supplies forged metal parts to many different industries all throughout the world. These industries include: architectural, door and window, marine, plumbing, pump, valve, hydraulic, electrical, gas and sporting equipment industries as well as many others.
CQueenta excels in supplying the best quality made metal forging for your application and at very competitive prices. Our qualified technical team offers ways to reduce your costs by 20% or more and also offers you a one stop shop for all your metal parts.
Advantages of Forged Parts (Closed Die Forged Parts)
One of the best-kept secrets in metal technology is the Forging process because of it near net shape and good surface condition. If you are machining more than 40% of your metal bar stock away, then forgings are for you and they will reduce your overall piece cost. You will not be machining away full price metal creating scrap shavings and you will save time. Custom metal forgings offer tremendous advantages over other manufacturing methods such as extrusions, castings, and machining from bar stock. If your company is not benefiting from these advantages, they should be - here is why!
Extensive Cost Savings
Across the Board Time Savings
Significant Product Improvements
Innovative Manufacturing Enhancements
High Strength
In making forged metal parts, the metal is worked twice under both tremendous pressures, first during rod extrusion/drawing or rolling and then during the close die forging process. The double working of metal under pressure compresses the metal and produces a very dense and refined grain structure. The tensile strength of the forged metal parts is thereby increased, and resistance to impact and abrasion is enhanced.
Leak Resistance
The dense, non-porous aspect of forged metal parts permits the designer to specify thinner sections without the risk of leaks due to flaws and voids. Often the thinner forged metal parts result in lighter weight and lower piece cost compared to other manufacturing processes.
Close Tolerances
Custom metal forgings produced in a steel die with close tolerances offers several advantages. Overall part dimensions are held closer than in sand casting. Dimensions show minimum variation from part to part and permit automatic chucking and handling in subsequent machining and assembly operations. The precise designs on the die surface can produce sharp impressions or depressions on the forging surface for company id or name, which is normally not the case with other forming processes.
Low Overall Cost
Mass production of forged metal parts lends itself to maximum savings. However, smaller quantities of copper alloy forgings can also prove economical. As mentioned forgings have good leak integrity, close tolerances, high strength with low weight, and designs with a non-symmetrical shape.
Forgings have superior surface condition compared to castings and therefore good for surface coating treatments like chrome or nickel plating, various painting options and anodizing.
For precise, strong, high-quality metal parts, choose Queenta as your partner for custom metal forging.
Request a quote or
contact Queenta to schedule a consultation.
Our Forging Procedure
The first step in producing a good quality forging involves the cutting of slugs (billets) from round, square or special shaped bar by sawing to the desired length of metal to fill the die. The slugs (billets) are then heated to forging temperature for the specific alloy. After heating, the slug is placed with tongs or special automatic/robotic clamp on the bottom forging die on the forging press. The action of the press is to then move rapidly downward with top die in place and slams down on the billet. The press exerts tremendous pressure, squeezing the metal into the shape of both die cavities and causing the forged metal parts to take form. This action also imparts strength to the part and refines the grain structure.
When forging a part, there is always excess metal that comes out of the two cavities where they close together. Therefore, the mass of the billet is more than the part so that the two die cavities will be completely filled. As the part takes shape under pressure, the excess metal is squeezed out into a "gutter" around the die cavities. Excess metal, is called "flash" and remains attached to the forging when it is ejected from the die. The flash is later removed by a trimming die operation to remove most all of the flash and this is normally performed on a punch press. Once trimmed, the forging is then finished. However, it can now be acid treated or shot blast to enhance the surface finish. If
machining is required, the forged part can easily be turned, drilled, tapped, milled, etc.
Metal Forging Presses
Queenta's forging presses range in size from 45 tons to 1600 tons and our technology ranges from mechanical crank to friction screw. Heating is either gas or electric depending on the alloy being forged.
Cold forging has also been used to manufacture aluminum alloy forgings. Totals of 47 forging presses as well as other state of the art equipment are used to produce over 10,000 different components in large or small runs.
Automation is used to facilitate high output rates for volume items, while difficult products with technical challenges are manufactured using manual operations. Let us add you to the list of our satisfied customers!
Request a quote on custom metal forgings, or
contact Queenta contact Queenta to learn more.
How Forgings compare to Castings
Forged metal parts are stronger. Hot and cold working strengthens parts in a way that casting can't match. Forged metal forgings surpass castings in predictable strength properties, producing superior strength for every part -- guaranteed.
Forging refines defects from cast ingots or continuous cast bar used to cut into billets. A casting has neither grain flow nor directional strength and is always subjectable to gassing (Porosity). The casting process cannot prevent formation of certain metallurgical defects and surface imperfections. Pre-working forge stock produces a grain flow oriented in directions requiring maximum strength. Dendritic structures, alloy segregations and like imperfections are refined in forging. Forgings are do not have porosity so are sound throughout the part!
Forged metal parts are more reliable, less costly. Casting defects occur in a variety of forms. Because hot working refines grain pattern and imparts high strength, ductility and resistance properties, forged products are more reliable and have less imperfections. And they are manufactured without the added costs for tighter process controls and inspection that are required for casting.
Custom metal forgings offer better response to heat treatment. Castings require close control of melting and cooling processes because alloy segregation may occur. This results in non-uniform heat treatment response that can affect straightness of finished parts. Forged metal parts respond more predictably to heat treatment and offer better dimensional stability.
Forging is flexible, cost-effective production that adapts to demand. Some castings, such as special performance castings, require expensive materials and process controls, and longer lead times. Open-die and ring rolling are examples of forging processes that adapt to various production run lengths and enable shortened lead times. Once tooling is in place, Close Die Forgings are quickly produced.
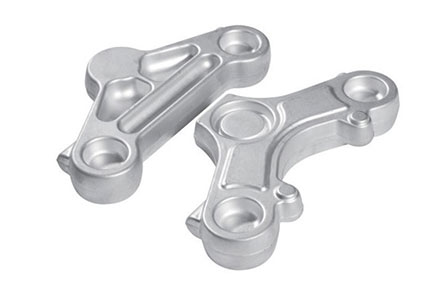
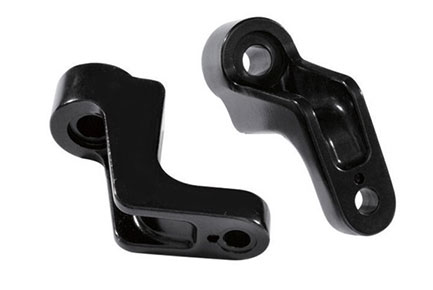